Design of nanocomposite materials requires a combination of intensive inputs, from both simulations and experiments, all occurring at and across multiple size scales. Atomic force microscopy (AFM) provides structural and mechanical information across the smaller end of these scales.
However, AFM can be laborious and error prone without understanding and utilizing the best practices available for the technique. We have surveyed the literature to compare, contrast, and summarize the current best practices for nanomechanical AFM of pure and heterogeneous polymer systems, and produced a comprehensive review of the topic, including recommendations for how to reliably and accurately operate an AFM instrument to collect nanomechanical information.
We are also interested in optimal experimentation more broadly, to maximize the information and utility of each individual (best-practices) AFM experiment. We are pursuing Bayesian and active learning approaches to design of experiments, including (semi-)autonomous laboratory concepts, with the goal of demonstrating improvements in research output and impact.
In pursuit of more accurate local modulus measurement, we developed a new modality of force-curve-based AFM that eliminates systematic bias in the calculation of elastic modulus due to cantilever spring constant calibration errors in force curve analysis. We showed that the ratio between the probe deflection and substrate indentation has important implications for the uncertainty of modulus measurement when using generalized adhesive Hertzian indentation models. This error analysis codifies the widely understood rule-of-thumb tradeoff that must be made: if the cantilever deflection is much greater than the material indentation, bias due to error in cantilever calibration will be amplified, whereas if the cantilever deflection is much smaller than material indentation, photodetector noise will dominate. For example, attempts to measure the modulus of a stiff material with a very compliant probe result in a high indentation ratio and a large systematic error due to deflection sensitivity calibration. Our work revealed that, under the common calibration methods which involve the equipartition theorem, a special, “magic” indentation ratio appears between these limits with the ability to annihilate spring constant calibration error.
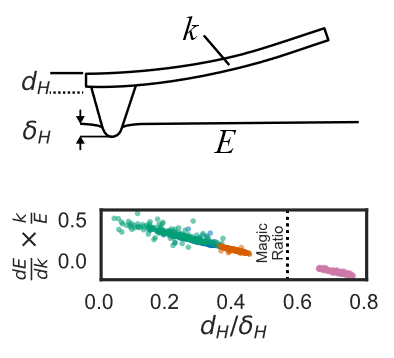
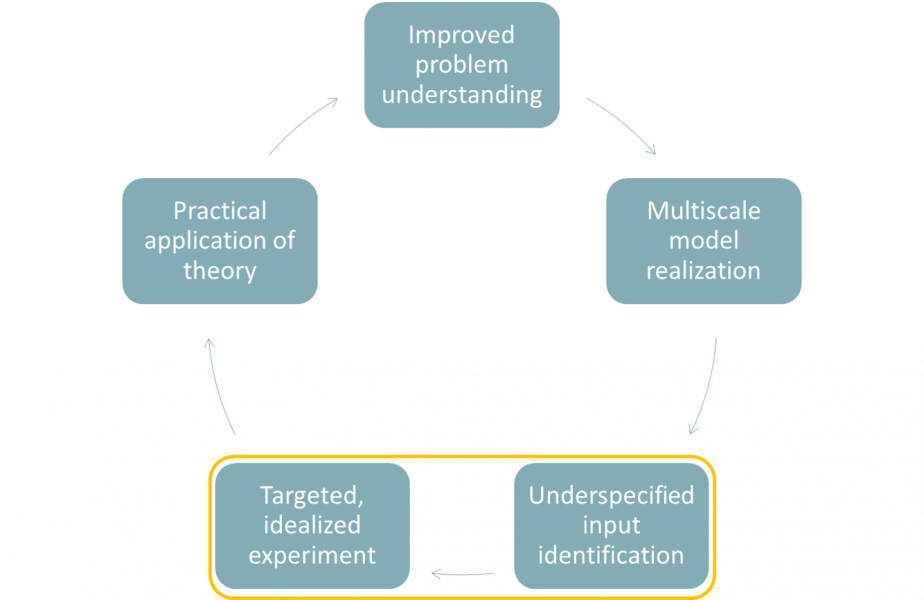
Active Researcher on the Project:
Relevant Publications
[1] Collinson, D. W., Sheridan, R. J., Palmeri, M. J., & Brinson, L. C. (2021). Best practices and recommendations for accurate nanomechanical characterization of heterogeneous polymer systems with atomic force microscopy. Progress in Polymer Science, 101420.
[2] Sheridan, R. J., Collinson, D. W., & Brinson, L. C. (2020). Vanishing Cantilever Calibration Error with Magic Ratio Atomic Force Microscopy. Advanced Theory and Simulations, 3(8), 2000090.